Episodes
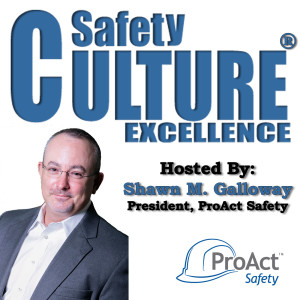
Monday Jan 14, 2019
576: Quantity and Quality
Monday Jan 14, 2019
Monday Jan 14, 2019

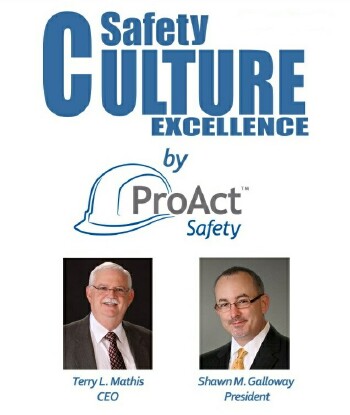
Wednesday Mar 04, 2015
Suppliers and Quality
Wednesday Mar 04, 2015
Wednesday Mar 04, 2015
W. Edwards Deming urged organizations to establish relationships with suppliers and stick with them, even when they could save a few pennies by changing to another. He knew that the reduced price was usually a loss leader and that the changeover would cost more than the savings. We have not yet learned this lesson in safety. We farm out services and products to the lowest bidder, assuming the quality is the same and that continuity of provider has no value. We also assume that a consultant who specializes in one service, or a manufacturer who specializes in a particular product, is superior. These assumptions are not necessarily so.
The relationship with a provider can make them more valuable than price, product or service. Someone who really takes the time to understand your business can often tailor to your needs much better than a subject-matter expert who doesn’t know or understand your organization. The relationship is often what gets you superior support, preferential treatment and customized solutions. Look for someone who cares for you, not just who gives you the lowest price. Quit trying to save pennies and concentrate on saving lives.
-Terry L. Mathis
For more insights, visit
www.ProActSafety.com
Terry L. Mathis is the founder and CEO of ProAct Safety, an international safety and performance excellence firm. He is known for his dynamic presentations in the fields of behavioral and cultural safety, leadership, and operational performance, and is a regular speaker at ASSE, NSC, and numerous company and industry conferences. EHS Today listed Terry as a Safety Guru in ‘The 50 People Who Most Influenced EHS three consecutive times. He has been a frequent contributor to industry magazines for over 15 years and is the coauthor of STEPS to Safety Culture Excellence (2013, WILEY).
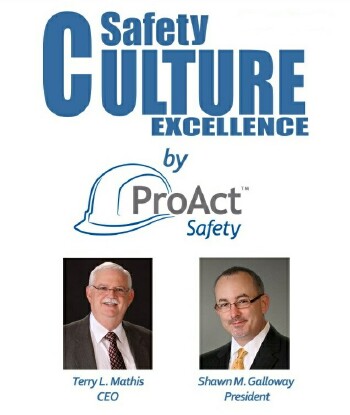
Wednesday Jan 21, 2015
Quantity and Quality
Wednesday Jan 21, 2015
Wednesday Jan 21, 2015
Rule of thumb: Any quantity goal without a quality requirement will encourage “pencil whipping”. This is especially true of safety audits and observations. Organizations that require everyone to do two observations per month or two audits per week are misstating what they truly want. Quantity is ineffective without quality. There are thousands of studies that support the idea that a certain quantity of contact or assessment is necessary for improvements. But they all go out the window if the numbers are filled with fake, or otherwise poor-quality, components.
What drives change is the right number of quality contacts. Going through the motions and getting the numbers just to check off a box is not what organizations really want. So why do they set these goals, omitting the quality requirements? Largely because the quantity is easily and discretely measured while the quality is more complicated and subjective. It is easier to create accountability around numbers than quality, but doing so can completely compromise the effort. State both quantity and quality requirements in all goals and do your best to hold workers accountable for both.
-Terry L. Mathis
For more insights, visit
Terry L. Mathis is the founder and CEO of ProAct Safety, an international safety and performance excellence firm. He is known for his dynamic presentations in the fields of behavioral and cultural safety, leadership, and operational performance, and is a regular speaker at ASSE, NSC, and numerous company and industry conferences. EHS Today listed Terry as a Safety Guru in ‘The 50 People Who Most Influenced EHS three consecutive times. He has been a frequent contributor to industry magazines for over 15 years and is the coauthor of STEPS to Safety Culture Excellence (2013, WILEY).
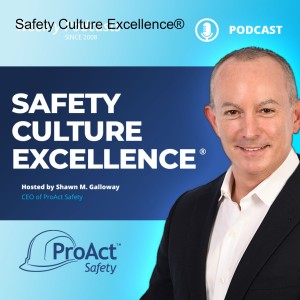
Monday Oct 10, 2011
202 - Five Steps to Sustainable Safety Culture Excellence
Monday Oct 10, 2011
Monday Oct 10, 2011
Greetings everyone, this podcast recorded while working in Menomonie, WI. For the podcast this week I’d like to share an article I wrote that was published in the September 2011 edition of BIC Magazine. It was titled “Five Steps to Sustainable Safety Culture Excellence”. The published article can either be found at www.BICALLIANCE.com or under Insights at www.ProActSafety.com.
I hope you enjoy the podcast this week. If you would like to download or play on demand our other podcasts, please visit the ProAct Safety’s podcast website at: http://www.safetycultureexcellence.com
Have a great week!
Shawn M. Galloway
ProAct Safety, Inc