Episodes
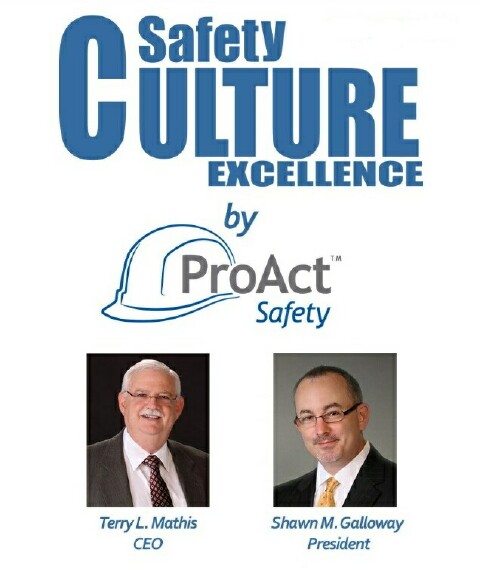
Wednesday Mar 26, 2014
Can-Do Safety Cultures
Wednesday Mar 26, 2014
Wednesday Mar 26, 2014
It is important to define the desired capabilities of a culture instead of simply the desired characteristics. What a culture “can do” is much more crucial than what it “is like.” That said, some cultures become can-do cultures without internalizing safety as a part of what they can do. Such cultures become “get it done at all costs” cultures. The members of the culture become willing to give their bodies up for the team. They put job completion ahead of all other priorities.
The history of a site can be a major influence in developing such a culture. Sites that have experienced multiple downsizing or threats of closing tend to develop work groups that perform for survival. The constant threat of being laid off or having your workplace closed tends to outweigh the threat of personal injury. If managers and supervisors constantly use these threats to motivate or hurry workers, the perception that production trumps safety is constantly reinforced.
When companies downsize, reorganize or otherwise disrupt site cultures, they should anticipate and manage the safety aspects of the change. Survival is an economic necessity, but poor safety can impact a site’s viability as much as ineffective or incomplete work. Survival mode should include both surviving the economic challenges and the safety issues. Again, it is not a dichotomy between production and safety, but addressing the need for safe production.
-Terry L. Mathis
Terry L. Mathis is the founder and CEO of ProAct Safety, an international safety and performance excellence firm. He is known for his dynamic presentations in the fields of behavioral and cultural safety, leadership, and operational performance, and is a regular speaker at ASSE, NSC, and numerous company and industry conferences. EHS Today listed Terry as a Safety Guru in ‘The 50 People Who Most Influenced EHS in 2010, 2011 and 2012-2013. He has been a frequent contributor to industry magazines for over 15 years and is the coauthor of STEPS to Safety Culture Excellence, 2013, WILEY.