Episodes
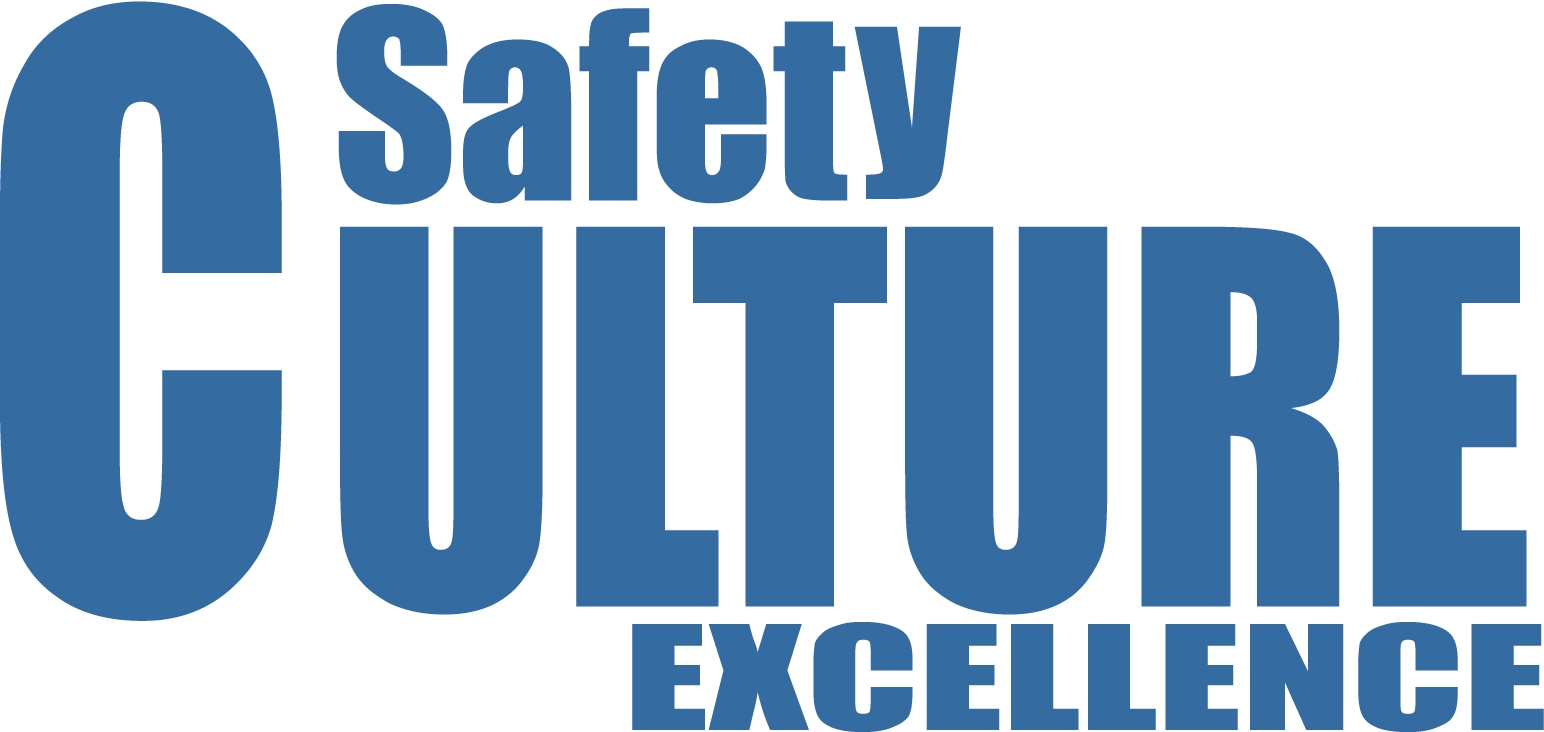
Wednesday Sep 25, 2013
Personal Responsibility for Safety
Wednesday Sep 25, 2013
Wednesday Sep 25, 2013
An article in the newspaper reported how many toddlers were backed over in their own driveways by their own parents and relatives. The closing call to action was for the government to pass legislation making backup cameras mandatory on all vehicles. While the intention is probably sincere, the method is flawed. We have progressed farther in industrial safety than we have in off-the-job safety and should take the lessons we have learned and apply them to problems such as these.
We addressed backing issues in industry successfully as much as 30 years ago, long before we ever started putting cameras on vehicles. We solved these problems through training and new procedures rather than through conditional fixes. The problem begins with the fact that driving has become so routine for most Americans that they have lost their sense of vulnerability. They view driving as a chore, a convenience, a necessity of daily life and not as the dangerous activity it actually is. Driving-related injuries and deaths still outnumber industrial ones by about a ten-to-one ratio. But we do not publicize this fact nor do we adequately train or prepare drivers to appreciate and address the risks of driving.
Certainly we should make conditions as safe as possible. Cars can be better equipped and driveways and roadways can be better designed for safety. But there will always be the need for more, and that more is for operators of vehicles to make sure they know what is in their path before they drive. The problem is not backing, it is checking before you back. Until drivers take personal responsibility to change their pre-driving routine the problem will persist regardless of the gadgets we attach to vehicles. We learned this already in industry and should not need to repeat the learning cycle before ending these tragedies.
-Terry L. Mathis
Terry L. Mathis is the founder and CEO of ProAct Safety, an international safety and performance excellence firm. He is known for his dynamic presentations in the fields of behavioral and cultural safety, leadership, and operational performance, and is a regular speaker at ASSE, NSC, and numerous company and industry conferences. EHS Today listed Terry as a Safety Guru in ‘The 50 People Who Most Influenced EHS in 2010, 2011 and 2012-2013. He has been a frequent contributor to industry magazines for over 15 years and is the coauthor of STEPS to Safety Culture Excellence, 2013, WILEY.
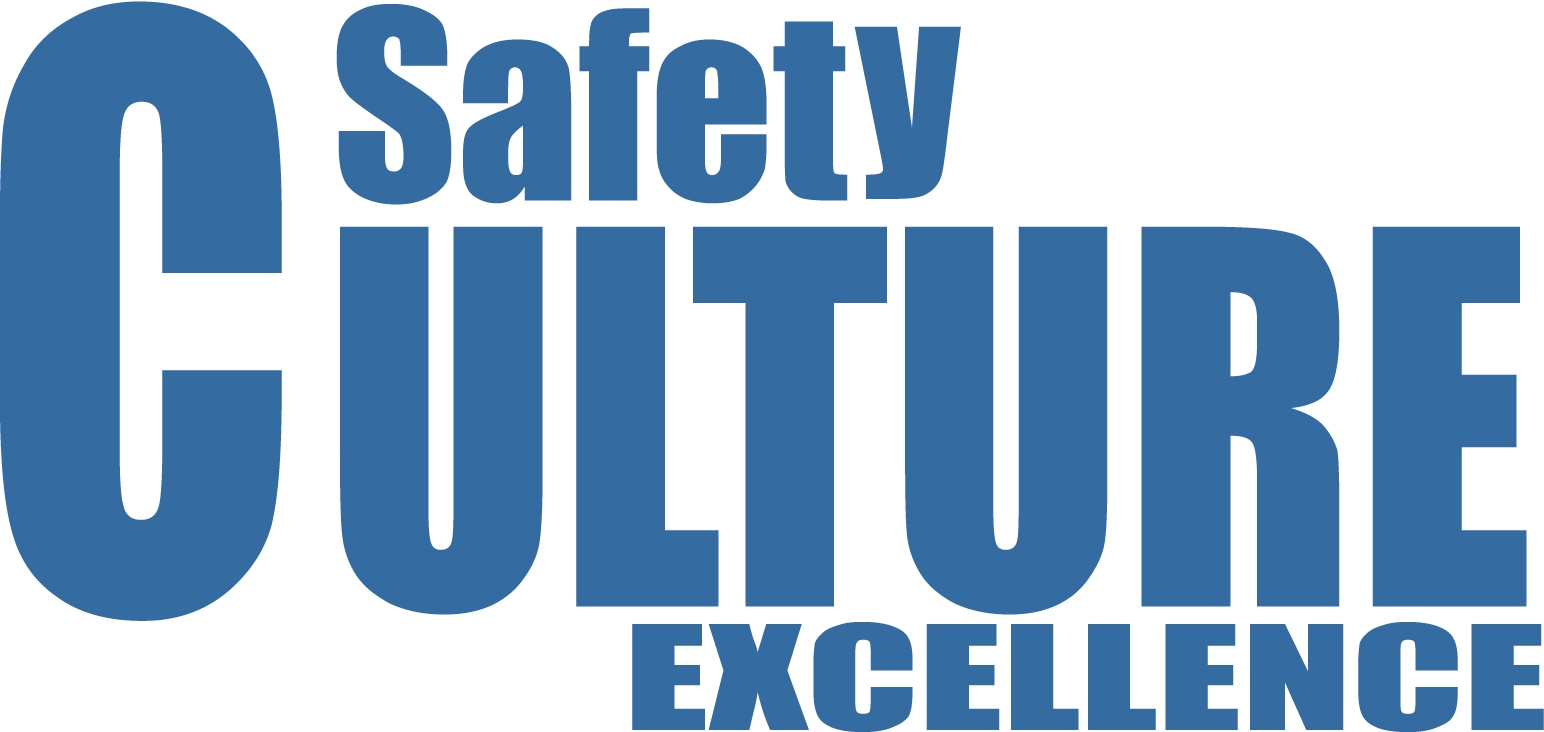
Wednesday Sep 18, 2013
More is Not Better: Only Better is Better
Wednesday Sep 18, 2013
Wednesday Sep 18, 2013
When safety results are unsatisfactory, managers tend to say, “We are not doing enough for safety.” There is an assumption that more effort will produce better results. In the short term this often seems true. When leaders focus on one priority over others, followers tend to direct their efforts accordingly. Leaders assume that their additional activities produced the desired results. Often, it was not the effort but simply the priority that drove the improvement. However, such knee-jerk reactions rarely work long term. Sustainable results depend more on the quality rather than the quantity of effort.
One organization increased the hours workers spent in classroom training because they discovered knowledge deficits had contributed to accidents. Accident rates reduced in the short-term, but knowledge levels did not rise. The emphasis on reducing accidents had focused worker efforts, but the training had not been effective in improving knowledge. Leaders realized after some investigation that the problem was the quality of the training. The training did not address the most critical knowledge needed. Increasing the quantity of the poorly designed training had simply subjected workers to more meaningless and ineffective activity. When the quality of the training was improved, more quantity was not needed.
Many organizations purchase the latest fads in safety training and programs in hopes of improving results. Again, there is this assumption that more is better. Rather than improving existing programs and training and aligning them with a better safety strategy, let’s simply do more. Unfortunately,” more” doesn’t fix ”poor.”
Very few organizations are failing to dedicate enough effort to safety, but many are not using that effort to its maximum effectiveness. The answer is not more effort; but better effort.
-Terry L. Mathis
Terry L. Mathis is the founder and CEO of ProAct Safety, an international safety and performance excellence firm. He is known for his dynamic presentations in the fields of behavioral and cultural safety, leadership, and operational performance, and is a regular speaker at ASSE, NSC, and numerous company and industry conferences. EHS Today listed Terry as a Safety Guru in ‘The 50 People Who Most Influenced EHS in 2010, 2011 and 2012-2013. He has been a frequent contributor to industry magazines for over 15 years and is the coauthor of STEPS to Safety Culture Excellence, 2013, WILEY.
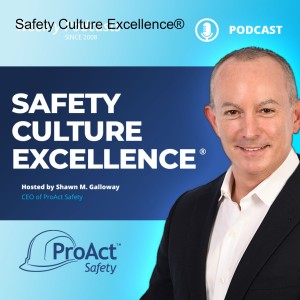
Monday Sep 16, 2013
307 - You Need to Manage Strategically
Monday Sep 16, 2013
Monday Sep 16, 2013
Greetings everyone, this podcast recorded while in Orange, Texas. I’d like to share an article I wrote, published June 2013 in ISHN Magazine. It was titled, You Need to Manage Strategically. The published article can either be found on the magazine’s website or under Insights at www.ProActSafety.com. I hope you enjoy the podcast this week. If you would like to download or play on demand our other podcasts, please visit the ProAct Safety’s podcast website at: http://www.safetycultureexcellence.com. If you would like access to archived podcasts (older than 90 days – dating back to January 2008) please visit www.ProActSafety.com/Store. For more detailed strategies to achieve and sustain excellence in performance and culture, pick up a copy of our book, STEPS to Safety Culture Excellence - http://proactsafety.com/insights/steps-to-safety-culture-excellence Have a great week! Shawn M. Galloway ProAct Safety, Inc
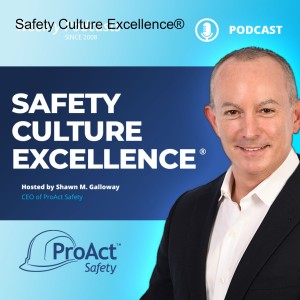
Monday Sep 09, 2013
306 - Overcoming invulnerability to strengthen safety culture
Monday Sep 09, 2013
Monday Sep 09, 2013
Greetings everyone, this podcast recorded while in Bethesda, Maryland. I’d like to share an article I wrote, published June 2013 in BIC Magazine. It was titled, Overcoming invulnerability to strengthen safety culture. The published article can either be found on the magazine’s website or under Insights at www.ProActSafety.com.
I hope you enjoy the podcast this week. If you would like to download or play on demand our other podcasts, please visit the ProAct Safety’s podcast website at: http://www.safetycultureexcellence.com. If you would like access to archived podcasts (older than 90 days – dating back to January 2008) please visit www.ProActSafety.com/Store. For more detailed strategies to achieve and sustain excellence in performance and culture, pick up a copy of our book, STEPS to Safety Culture Excellence - http://proactsafety.com/insights/steps-to-safety-culture-excellence
Have a great week!
Shawn M. Galloway
ProAct Safety, Inc
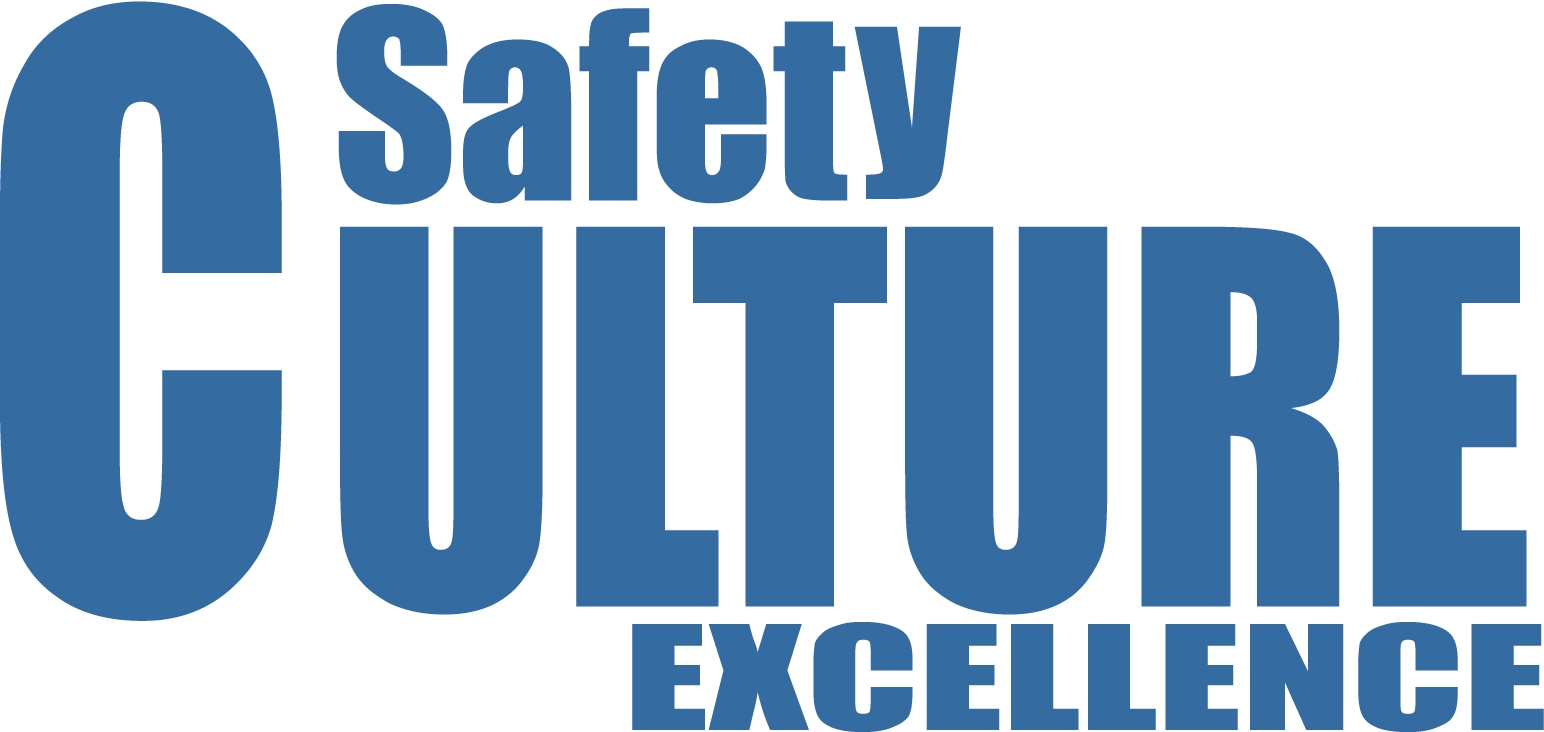
Wednesday Sep 04, 2013
Cultural Compliance: A Step Short of Excellence
Wednesday Sep 04, 2013
Wednesday Sep 04, 2013
What if everyone in your organization obeys the rules, follows the procedures and wears their PPE with a minimum of supervision or management? Is this safety culture excellence? NO! This is a culture of compliance, not excellence. Certainly, it is a move in the right direction and is a desirable accomplishment. It is a step above command-and-control but still a number of steps short of true excellence.
Excellence is well above and beyond simple compliance. Most rules and procedures are minimal standards for safety and only address the most common and obvious risks. Even organizations which reach high levels of compliance still have a level of accidents untouched by their efforts. As organizations begin to plateau in their compliance efforts, they often look for advanced strategies to help them accomplish the next step change.
Beyond compliance, workers must think and act intelligently; not just mindlessly comply. Organizations must examine their influences on workers to make sure they reinforce safety and not shortcuts or acceptance of risks. When all factors, both individual and organizational are aligned to go above and beyond compliance, the potential for excellence begins. At this level of performance, compliance is so basic that is expected of everyone all the time. The new measure of success is repeated victories, not simply playing a decent game.
-Terry L. Mathis
Terry L. Mathis is the founder and CEO of ProAct Safety, an international safety and performance excellence firm. He is known for his dynamic presentations in the fields of behavioral and cultural safety, leadership, and operational performance, and is a regular speaker at ASSE, NSC, and numerous company and industry conferences. EHS Today listed Terry as a Safety Guru in ‘The 50 People Who Most Influenced EHS in 2010, 2011 and 2012-2013. He has been a frequent contributor to industry magazines for over 15 years and is the coauthor of STEPS to Safety Culture Excellence, 2013, WILEY.
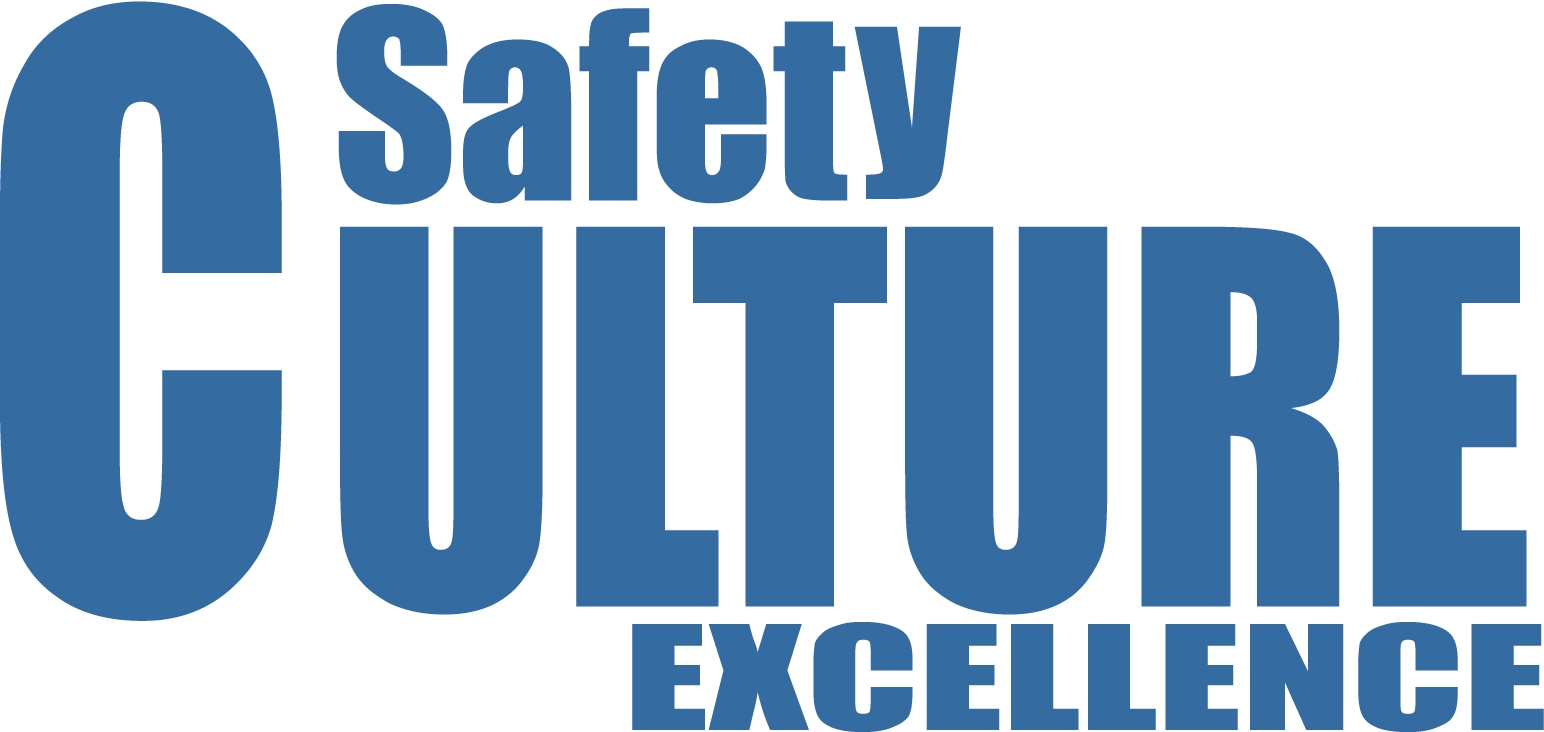
Wednesday Aug 28, 2013
Lateral Communication
Wednesday Aug 28, 2013
Wednesday Aug 28, 2013
When we talk to most executives about effective safety communication, they instantly focus on the vertical information (i.e., what flows from leaders to the workers and what workers send back to leaders). Vertical communication can happen directly, through various communication media, or through the usual organizational levels person-to-person. While this vertical information is important, so is lateral communication: what goes between workers and other workers.
Safety engagement and behavioral programs often attempt to increase and/or improve lateral communication. Regardless of whether you are using such a program or simply wanting to improve, if you want your workers to talk effectively to each other about safety, you should address the following issues:
1) Conversations between workers should be focused on improvement targets, not just common practice. Targeted improvements create legitimate talking points and create discrete dichotomies of “did you do this” or “did you not do this?” Having workers simply evaluate each others performance more often leads to disagreement than improvement. Remember to consider targeting improvements in safety culture as well as accident prevention.
2) The model for conversations should be one of coaching rather than confrontation. Confrontation creates enemies who disagree. Coaching creates allies in change.
The goals of lateral conversations should be to, A) Encourage those working toward improvement, or B) To discover what is influencing or blocking improvements in those observed not meeting improvement goals.
Often the best way of discovering such issues is simply to ask “Why?” or “Why not?” when a fellow worker is not doing the targeted precaution. Approaches that follow these guidelines more often prove successful.
-Terry L. Mathis
Terry L. Mathis is the founder and CEO of ProAct Safety, an international safety and performance excellence firm. He is known for his dynamic presentations in the fields of behavioral and cultural safety, leadership, and operational performance, and is a regular speaker at ASSE, NSC, and numerous company and industry conferences. EHS Today listed Terry as a Safety Guru in ‘The 50 People Who Most Influenced EHS in 2010, 2011 and 2012-2013. He has been a frequent contributor to industry magazines for over 15 years and is the coauthor of STEPS to Safety Culture Excellence, 2013, WILEY.
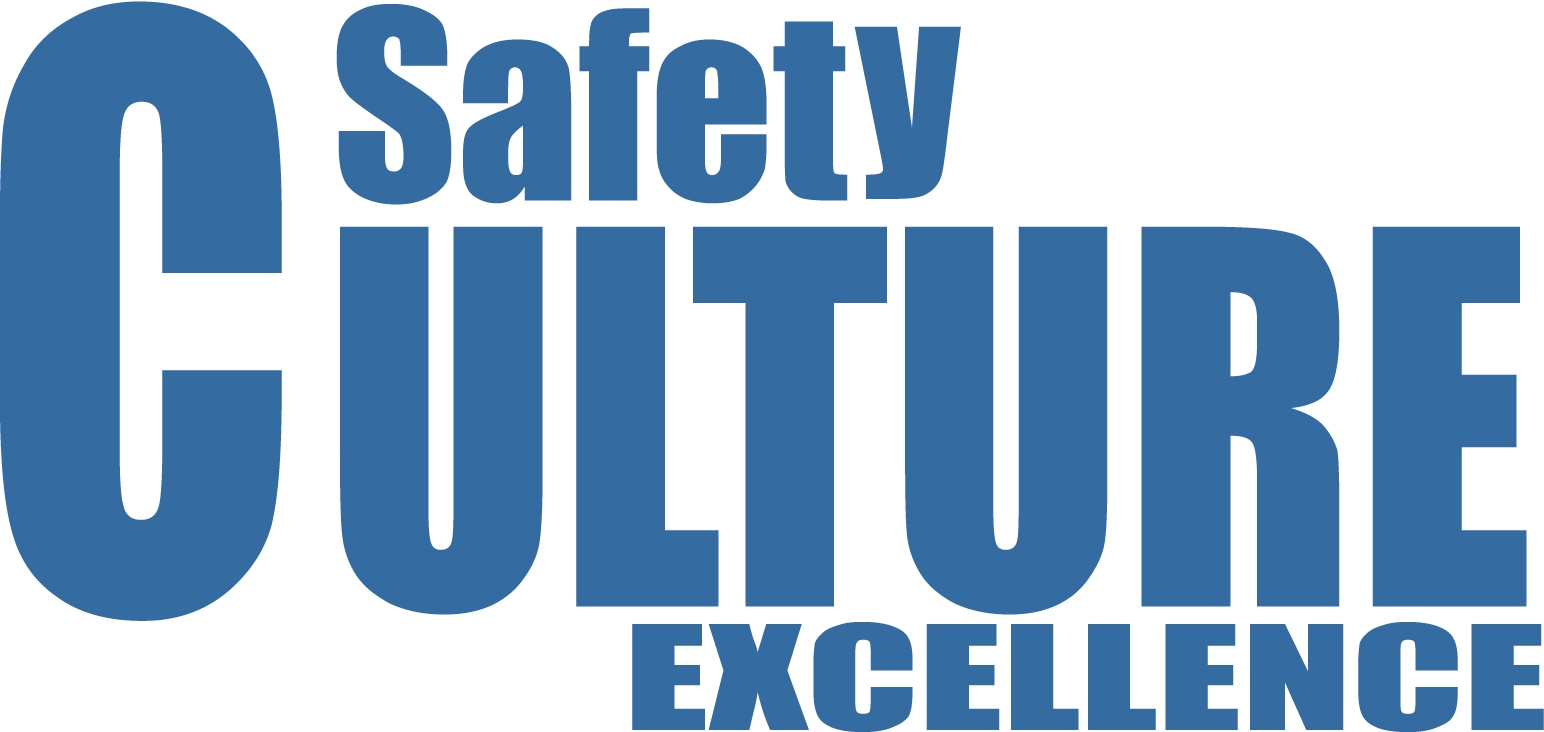
Friday Aug 23, 2013
Safety’s “Usual Suspects”
Friday Aug 23, 2013
Friday Aug 23, 2013
In the classic movie, Casablanca, whenever a crime took place the police gathered up the “usual suspects” to show that they were taking action. The usual suspects regularly got blamed but were seldom the true guilty parties. At the end of the movie, even when they were sure of who committed the crime, they simply went through the motions to satisfy those in control...Investigating industrial accidents can fall into the same trap of substituting action for results.
When reading over a recent set of accident investigation forms, I was alarmed at the cut-and-paste wording that seemed to repeat in so many of them. Corrective actions almost always were the same: either change a condition or blame an individual by imposing discipline or retraining. There were no influences or barriers mentioned. It was as if all accidents were caused strictly by conditions or negligence.
Theoretically, neither a condition nor a behavior can be a true “root cause” since they are both caused or influenced by other factors. Conditions don’t cause themselves and behaviors are not always simply the choice of the individual involved. All this emphasizes the need to ask the question “Why?” when investigating accidents. Why was there an oil spill on the floor? Why did you use pliers instead of a wrench? Without getting to the underlying causes we tend to take the easy action of fixing the blame on the usual suspects instead of truly fixing the problem.
-Terry L. Mathis
Terry L. Mathis is the founder and CEO of ProAct Safety, an international safety and performance excellence firm. He is known for his dynamic presentations in the fields of behavioral and cultural safety, leadership, and operational performance, and is a regular speaker at ASSE, NSC, and numerous company and industry conferences. EHS Today listed Terry as a Safety Guru in ‘The 50 People Who Most Influenced EHS in 2010, 2011 and 2012-2013. He has been a frequent contributor to industry magazines for over 15 years and is the coauthor of STEPS to Safety Culture Excellence, 2013, WILEY.
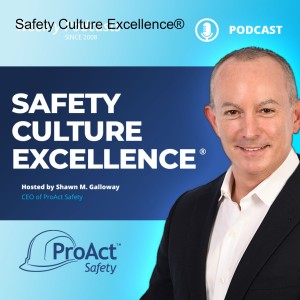
Monday Aug 19, 2013
303 - Safety leadership happens in the middle
Monday Aug 19, 2013
Monday Aug 19, 2013
Greetings everyone, this podcast recorded while in Wisconsin Dells, Wisconsin. I’d like to share an article I wrote, published May 2013 in BIC Magazine. It was titled, Safety leadership happens in the middle. The published article can either be found on the magazine’s website or under Insights at www.ProActSafety.com. I hope you enjoy the podcast this week. If you would like to download or play on demand our other podcasts, please visit the ProAct Safety’s podcast website at: http://www.safetycultureexcellence.com. If you would like access to archived podcasts (older than 90 days – dating back to January 2008) please visit www.ProActSafety.com/Store. For more detailed strategies to achieve and sustain excellence in performance and culture, pick up a copy of our book, STEPS to Safety Culture Excellence - http://proactsafety.com/insights/steps-to-safety-culture-excellence Have a great week! Shawn M. Galloway ProAct Safety, Inc
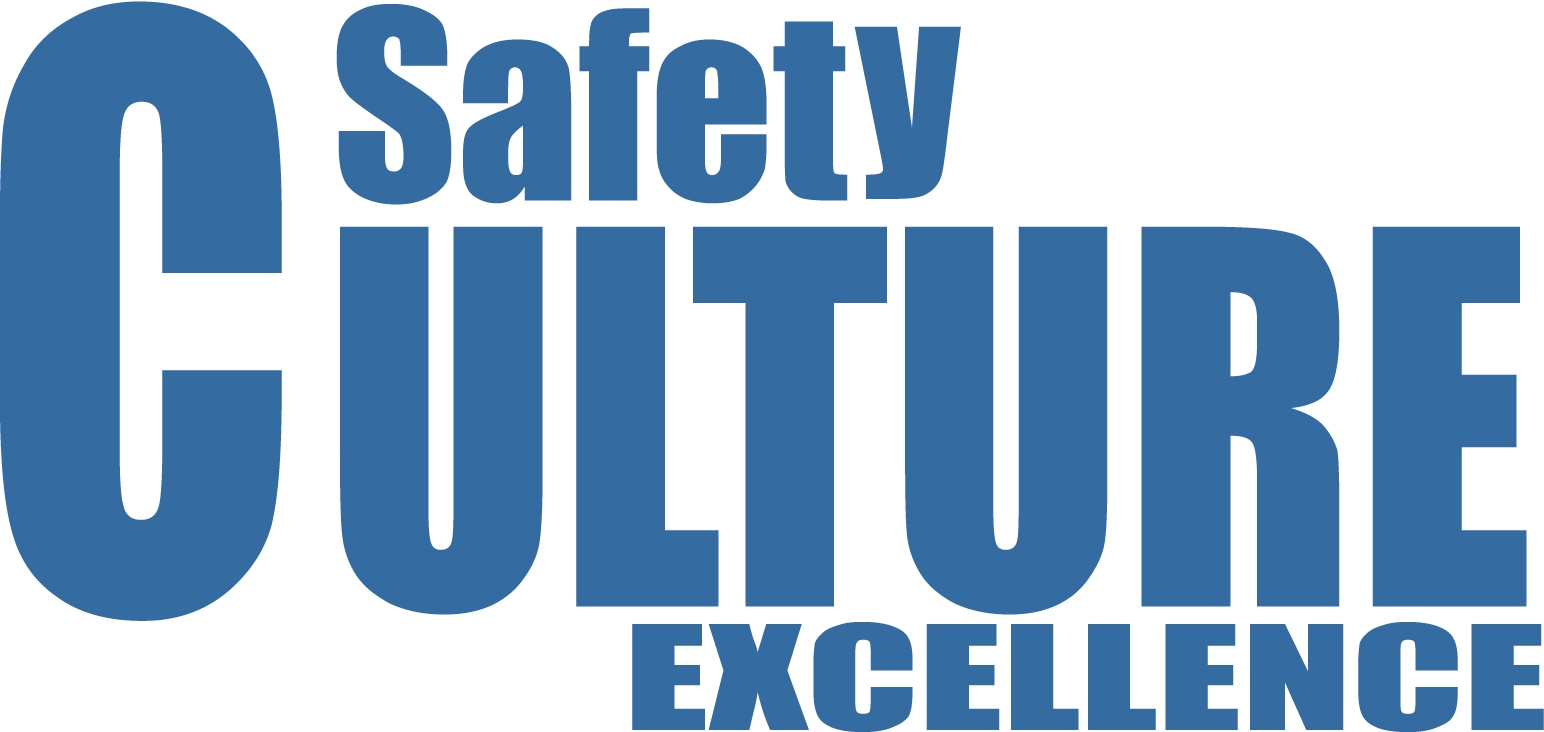
Wednesday Aug 14, 2013
Creating a Sense of Urgency
Wednesday Aug 14, 2013
Wednesday Aug 14, 2013
For many years business strategists suggested that cultures benefited from what they called “Positive Urgency.” Experimentation and research had shown that a sense of urgency caused otherwise complacent workers to rally around a cause and produce higher levels of action toward goals. To accomplish this end, leaders were urged to create artificial emergencies to challenge workers. These were called “burning platforms” and were designed to produce stress and a sense of crisis.
Slowly leaders and their experts realized that what people really do on burning platforms is to escape, not solve problems. They also do not continue their emergency behaviors after the emergency is over. A sense of urgency only creates a culture change if it is sustained over time and does not kill the members with stress before they change. The experts are now calling for more lasting and important and less urgent and artificial stimuli to create the desired sense of urgency.
In safety, it has historically been tragic accidents or bad trends in accident frequency that have caused us to become positively urgent. We react to disasters in safety as we do in business, by rallying and taking significant action. However, just like in business, when the severity and/or frequency goes away so does the increased action. The challenge in safety is to find these long-lasting reasons for significant action even when accidents are not providing them. This is the way to proactive excellence.
In business, they have turned to building a sense of identity, not just action. What will the organization be remembered for and is it important? Safety must find its own identity also. What does this safety culture seek to become and does that identity inspire significant action toward excellence? The answer may be different for different organizations, but the right answers will not be found unless the right questions are asked.
-Terry L. Mathis
Terry L. Mathis is the founder and CEO of ProAct Safety, an international safety and performance excellence firm. He is known for his dynamic presentations in the fields of behavioral and cultural safety, leadership, and operational performance, and is a regular speaker at ASSE, NSC, and numerous company and industry conferences. EHS Today listed Terry as a Safety Guru in ‘The 50 People Who Most Influenced EHS in 2010, 2011 and 2012-2013. He has been a frequent contributor to industry magazines for over 15 years and is the coauthor of STEPS to Safety Culture Excellence, 2013, WILEY.
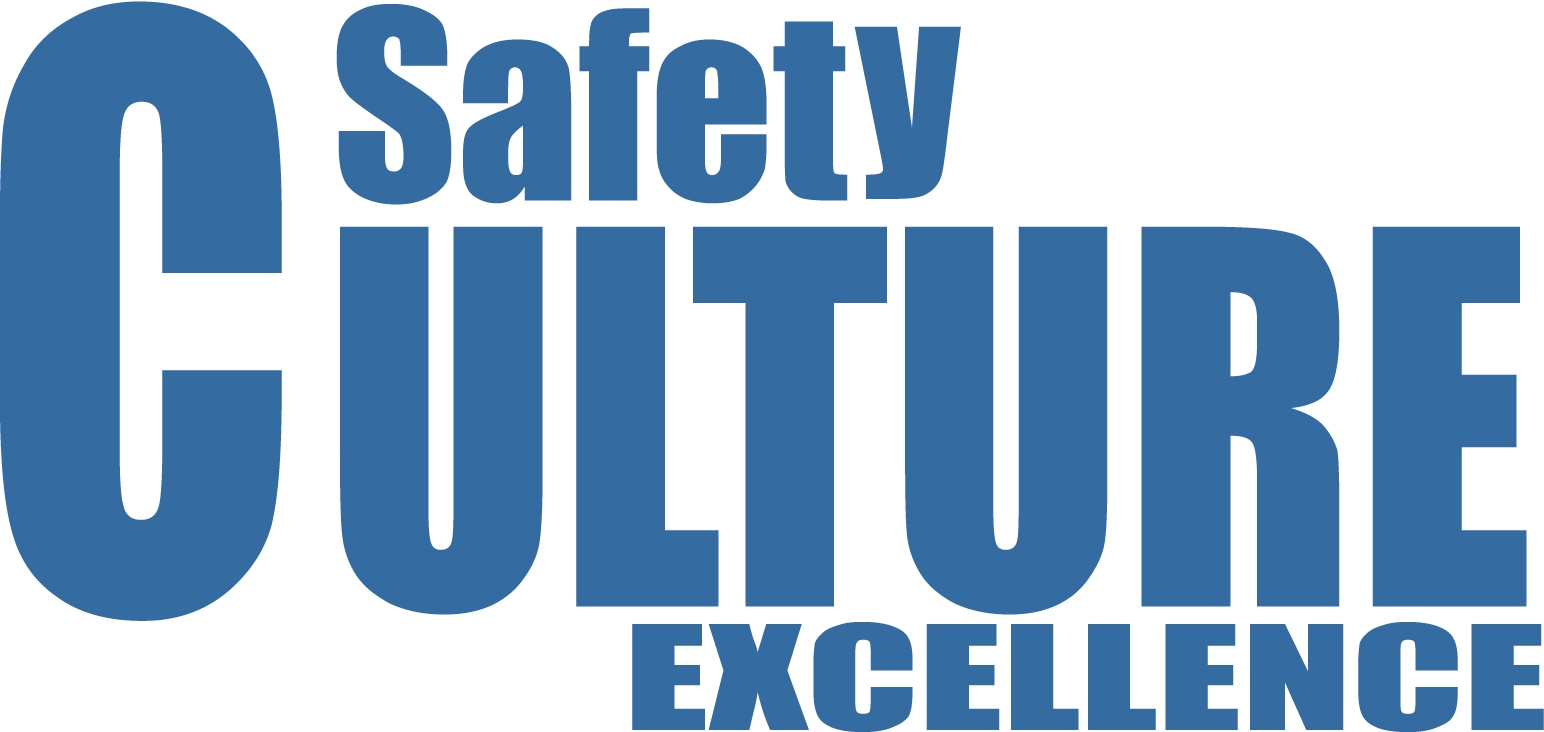
Wednesday Aug 07, 2013
Is Your Organization Oozing Expertise?
Wednesday Aug 07, 2013
Wednesday Aug 07, 2013
The US Census Bureau estimates that 35 million Baby Boomers will be leaving the workplace over the next 10 years or so. If you have these individuals in key positions and lose them all at once, how will that impact your organization? Will they take key safety information with them or will they pass it on before they retire? The answer to that may depend on your planning and the results may be significant.
Many Boomers have been in the same position for years; some for their whole careers. They have knowledge that is not always captured in operating manuals or other documentation. They also have developed judgment about how to handle certain situations based on their years of observation and experience. How can you keep this knowledge and judgment when you lose the people?
One answer is a mentoring program in which experienced workers train new workers. New workers can be asked to capture the tips and procedures they learn and share them with the next generation of workers. Another approach is to have experienced workers hold formal training, develop training materials, or lead JSA or JSOP teams. Still other organizations hire key retirees as part-time consultants or on-call resources for the new employees.
Whatever your plan, your goal should be to spare your organization from oozing out needed expertise as the new generation of workers replace the old.
-Terry L. Mathis
Terry L. Mathis is the founder and CEO of ProAct Safety, an international safety and performance excellence firm. He is known for his dynamic presentations in the fields of behavioral and cultural safety, leadership, and operational performance, and is a regular speaker at ASSE, NSC, and numerous company and industry conferences. EHS Today listed Terry as a Safety Guru in ‘The 50 People Who Most Influenced EHS’ in 2010, 2011 and 2012-2013. He has been a frequent contributor to industry magazines for over 15 years and is the coauthor of STEPS to Safety Culture Excellence, 2013, WILEY.